Los Ensayos No Destructivos (END) se han convertido en una herramienta esencial para evaluar la integridad estructural de equipos industriales y mineros, que constantemente están sometidos a condiciones extremas de temperatura y presión.
La inspección visual, el uso de tintas penetrantes, la prueba neumática, etc., son algunos END que permiten determinar el estado real de un equipo y evaluar fallos imprevistos sin comprometer su operatividad.
En este artículo, haremos una recopilación de los tipos de Ensayos No Destructivos utilizados en Sandora para obtener el diagnóstico de un componente, garantizar su correcto funcionamiento y evitar costosas fallas.
Ensayos No Destructivos
Los Ensayos No Destructivos (END) son un conjunto de técnicas y métodos que permiten evaluar la integridad y propiedades de materiales, componentes y estructuras de un equipo, sin afectar sus propiedades físicas, químicas o mecánicas.
Dichas técnicas son fundamentales en diversos sectores industriales, desde la fabricación hasta el mantenimiento, para garantizar la seguridad y confiabilidad de los productos:
¿Por qué son importantes los END?
- Detección temprana de defectos: Identificación de grietas, corrosión, delaminación, discontinuidades y otros defectos antes de que evolucionen y causen una falla catastrófica.
- Minimización de tiempos de parada: Al detectar problemas de manera proactiva, se evitan paradas no programadas y se reducen los costos de mantenimiento.
- Aumento de la vida útil: Un programa de END regular contribuye a prolongar la vida útil de los radiadores y otros componentes.
- Mejora de la seguridad: Al garantizar la integridad estructural, se reducen los riesgos para el personal y el entorno.
El alcance de estos objetivos no implica solo realizar una inspección estándar o una recolección de datos estadísticos; la clave está en aplicar una técnica acorde al equipo, a fin de garantizar la confiabilidad, la rentabilidad y el desempeño del activo durante el ciclo de vida.
En tal sentido, es importante considerar algunos criterios clave, como: tipo y origen de discontinuidad a ser detectada, norma de diseño, método de fabricación, datos operativos, accesibilidad a la región de ensayo, antecedentes históricos, costos asociados, entre otros.
Veamos a detalle los END más comunes:
Tipos de Ensayos No Destructivos
En la actualidad, existen numerosos tipos de Ensayos No Destructivos, los cuales están permanentemente en evolución.
Según la aplicación, los END se pueden clasificar en tres tipos, cada uno con ensayos característicos:
- Técnicas de inspección superficial, para comprobar la existencia de discontinuidades en la superficie de un material (inspección visual, partículas magnéticas, etc.).
- Técnicas de inspección volumétrica, para determinar discontinuidades internas (ultrasonidos, radiografía industrial, etc.).
- Técnicas de inspección de la integridad o hermeticidad, para detectar fugas de fluidos o gases en componentes o sistemas que deben mantener un vacío o una presión interna determinada (prueba de presión, prueba neumática, etc.).
Particularmente, Sandora dispone de diversos tipos de END para calificar la integridad de un equipo industrial o minero, prestando atención especial a cada detalle para lograr los mejores resultados:
Ensayos No Destructivos aplicados en SANDORA
1. Inspección visual
Forma parte de las técnicas de inspección superficial y consiste en un examen detallado de las áreas accesibles de un componente o pieza, a fin de detectar defectos exteriores (grietas, corrosión, abolladuras, deformaciones).
Para ello, es importante que la superficie a evaluar esté limpia, además de contar con buena iluminación, pues la pieza es examinada directamente al ojo o a través de algún instrumento visual (lupa, boroscopio, fibroscopio, etc.) y un inspector cualificado.
Generalmente, este ensayo se aplica para efectuar una evaluación general de un elemento, herramienta o componente y hacer una detección temprana de algún defecto.
2. Tintas penetrantes
Es una técnica de inspección superficial basada en la capilaridad de los líquidos, que permite su penetración y retención a través de discontinuidades superficiales abiertas (fisuras, grietas, poros, etc.).
Para ello, se aplica una tinta penetrante (de color rojo o fluorescente y baja viscosidad) en la superficie del componente, bien sea por inmersión (sumergir la pieza en un recipiente con el líquido), pulverización (por medio de un chorro de aire a baja presión) o con brocha.
Luego, se retira el exceso usando un líquido removedor y se aplica un revelador (que normalmente tiene talco en suspensión).
El líquido penetrante aprisionado en la discontinuidad de la pieza será absorbido por el revelador y dejará ver las discontinuidades existentes, con una indicación aproximada de la profundidad y tamaño del defecto.
Este ensayo es económico, muy fácil de aplicar y efectivo para identificar irregularidades en las soldaduras de los componentes.
Para su aplicación, se requiere que la superficie esté libre de cualquier tipo de contaminante (polvo, grasa, óxido, entre otros), que dificulte el procedimiento y afecte el resultado del ensayo.
Dato: El tiempo mínimo de penetración de un líquido viene determinado por el fabricante. En promedio, varía entre 5 y 30 minutos.
3. Inspección boroscópica
Constituye una técnica de inspección visual indirecta y se refiere al uso de un instrumento llamado «boroscopio» para inspeccionar el interior de áreas de difícil acceso (tuberías, cavidades, etc.), con el propósito de detectar defectos internos como corrosión, erosiones y depósitos.
Dicho instrumento puede ser rígido o flexible y poseen una sonda adaptada a una cámara digital y obtener imágenes directas de la condición interna.
El alcance de este ensayo está limitado por la longitud y diámetro del boroscopio utilizado y es aplicable en cualquier etapa del proceso productivo.
Si deseas profundizar en la importancia y la funcionalidad de este método, te recomendamos el artículo: Inspección Boroscópica: Control de Calidad en la fabricación.
4. Prueba neumática
Es una técnica destinada a evaluar la estanqueidad de un componente mediante la presurización del equipo con aire o un gas no tóxico e inerte (como el nitrógeno) y el monitoreo de la caída de presión respectiva.
Es un método eficaz para detectar fugas y requiere la inclusión de dispositivos de control y liberación de presión, para asegurar el bienestar de los operadores y evitar daños en el equipo.
5. Análisis termográfico
Representa un método de inspección que permite la medición de la temperatura radiada por un cuerpo desde una cierta distancia y sin contacto.
Esto ocurre cuando el flujo de calor en un cuerpo presenta anomalías, provocando contrastes de temperatura en su superficie (patrones térmicos) reconocibles por una cámara termográfica que capta la radiación infrarroja emitida para generar una imagen.
Gracias a ello, es posible detectar en tiempo real desbalances térmicos, sobrecalentamientos locales, obstrucciones que limitan el flujo del fluido y otros problemas relacionados con la transferencia de calor del componente.
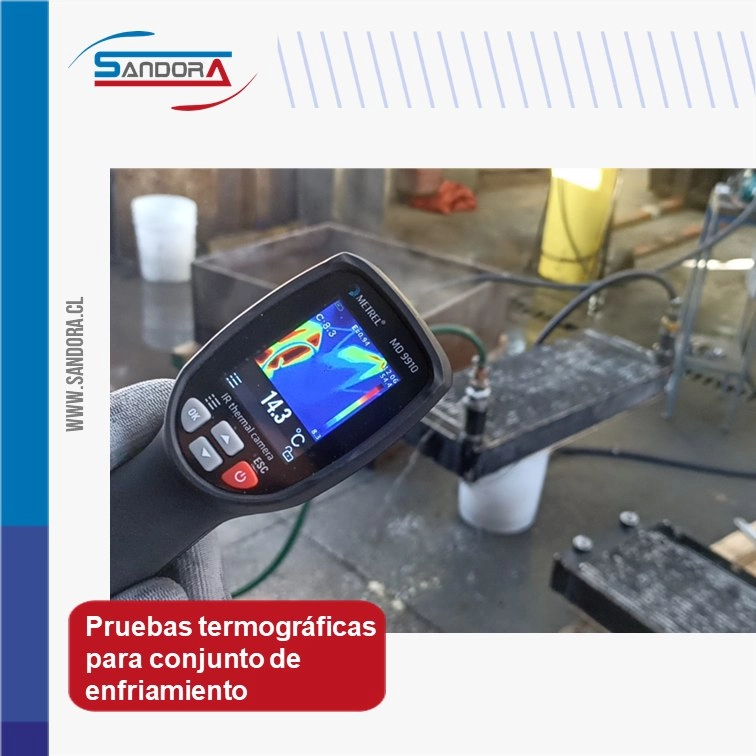
Según la energía calorífica transferida, este método se clasifica en:
- Termografía pasiva, si no se usa ninguna estimulación de calentamiento o enfriamiento externo para provocar un flujo de calor en el cuerpo inspeccionado.
- Termografía activa, si se requiere de una estimulación externa de la pieza a inspeccionar para provocar un flujo de calor (pulso de calor, fuentes de calor moduladas, entre otros).
- Vibrotermografía, si las imágenes se obtienen mediante ondas térmicas generadas por el sonido elástico o las ondas ultrasónicas.
Dato: El espectro infrarrojo se extiende desde el límite del rango visible hasta llegar a la región de las microondas. Sin embargo, existen dos regiones donde la transmisión es más elevada: la zona de 760‐2.000 nm (sistemas de onda corta) y la zona de 4.000‐10.000 nm (sistemas de onda larga).
6. Partículas magnéticas
La evaluación por partículas magnéticas es un ensayo útil para la localización de defectos superficiales y sub-superficiales en materiales ferromagnéticos (hierro, níquel, cobalto, etc.).
Su principio básico es el magnetismo y está basado en el hecho de que, cuando la pieza o componente a examinar es magnetizado, las discontinuidades existentes causan un campo de fuga en el flujo magnético, que puede ser detectado a través del uso de partículas ferro-magnéticas.
En ese sentido, para ser atraídas por el campo, las partículas aplicadas en la superficie deben poseer cualidades como alta permeabilidad, fuerza coercitiva baja y gran contraste, y pueden ser secas, húmedas o fluorescentes.
La aglomeración de las partículas en el contorno de la discontinuidad indica su localización, forma y extensión.
Este tipo de ensayo es aplicable en la inspección de soldaduras, el análisis de motores, poleas, rodamientos, estado de cojinetes, desalineamientos, etc.
Dato: Normalmente, son requeridas dos o más secuencias de operaciones en una misma región de una pieza y en diferentes direcciones.
En nuestra sección «Noticias» está disponible el artículo sobre Calidad Y Seguridad Reforzadas: Ensayos No Destructivos Por Partículas Magnéticas, con consideraciones relevantes del método y las ventajas que ofrece.
¡Al combinar diferentes técnicas de Ensayos No Destructivos, es posible obtener una evaluación completa de la condición de un equipo y tomar decisiones de mantenimiento basadas en datos reales!
En Sandora, nos dedicamos a garantizar calidad y precisión en cada etapa del proceso de inspección, desde la evaluación inicial hasta la entrega del informe final, mediante técnicas avanzadas centradas en mantener los equipos funcionando de manera impecable.
Echa un vistazo a esta evaluación efectuada a un tanque de combustible Komatsu 830E para un importante cliente:
Contáctanos y descubre todas nuestras soluciones para el sector industrial y minero.